SlurryMaster 8000 Display
SlurryMaster 8000 Display
No se pudo cargar la disponibilidad de retiro
SlurryMaster 8000 - Control without compromise
SlurryMaster 8000 is an easily operated system with an intuitive and userfriendly interface that ensures safe operation of the slurry tanker. The system is an autonomous system designed solely for the operation of a slurry tanker and therefore no compromises has been made which would have been the case if a more generally platform had been used. The system is a further development of the familiar SlurryMaster 6000 operating system.
Touchscreen
All displays/controls take place via a 10” high-resolution colour touchscreen which has been designed to require a minimum number of input steps in order to navigate in the system. The screen is based on standard PC technology. This future-proofs the investment since the system can easily be adjusted to the demands of tomorrow.
Implements
It is possible for the computer to store settings for up to 10 different implements. Each implement can be named and settings adjusted as required. The first time an implement is attached, the computer automatically runs a list of setup options. When the settings have been saved, they can be used the next time the implement is used. This reduces the time spent on changing implements.
Joystick
The essential functions for operating the loading systems and appliances are controlled via a newly developed and ergonomically designed joystick. The surface of the joystick is coated with silicone. All buttons have a back light and give a distinctive click when pressed. There is a hand rest on the pad and a firm grip for the buttons to ensure safe operation even when driving on rough surfaces.
Help screen for joystick
A single touch on the joystick icon at the top of the screen produces a list of the features which are available at the time of operation. The system is structured so that it will only show the functions that the machine is equipped with.
Customer jobs
The system can save up to 18 different jobs and has one seasonal counter. Data such as customer name, driver name, field number, etc., are logged for each job; this information can later form the basis for customer invoicing. When the job is completed, data can be saved onto a USB stick in Excel format or it can be printed out. Eventually, a customer database can be set up and various statistical analyses performed.
Service and troubleshooting tools
The system is fitted with several tools that make servicing and troubleshooting very easy. These include an error log that enables the localisation of periodic faults. This means that your authorized mechanic will identify the error more quickly and can make the machine running again.
Share
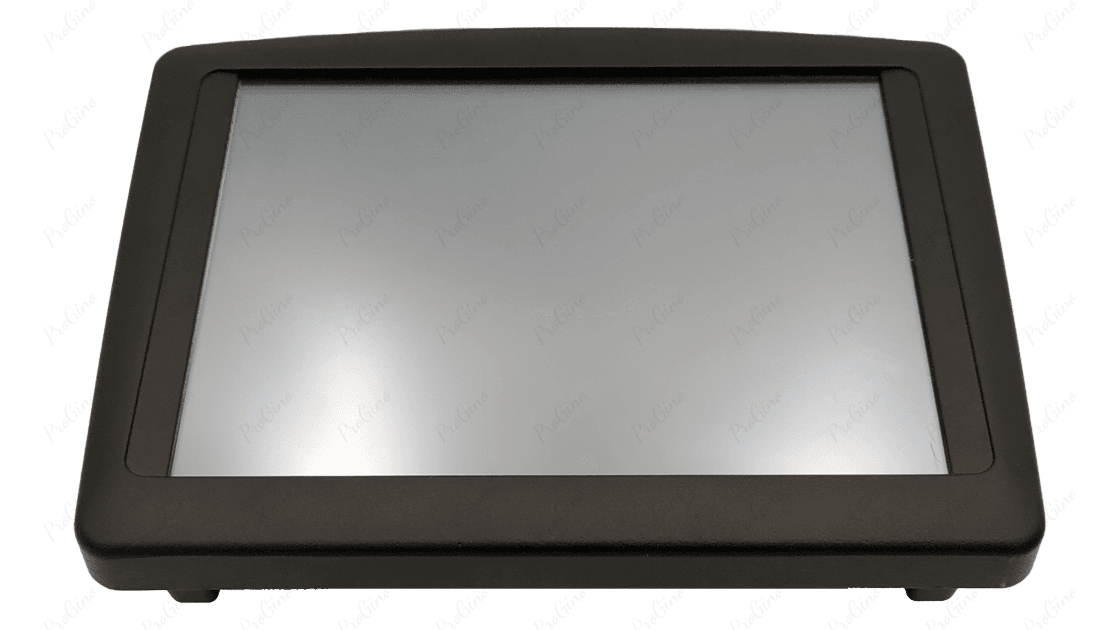
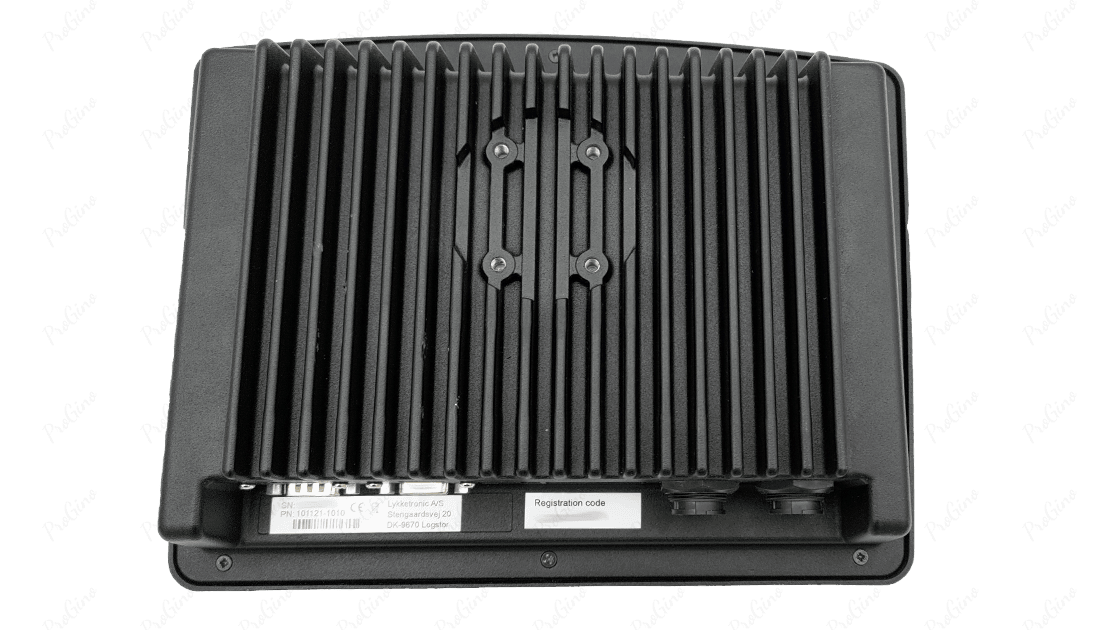

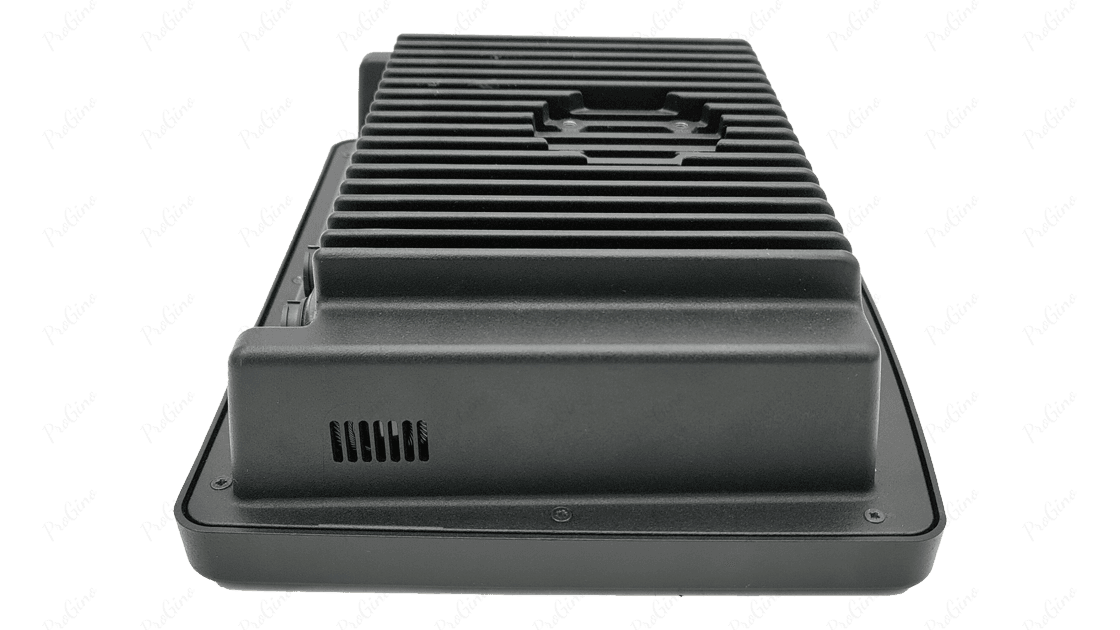
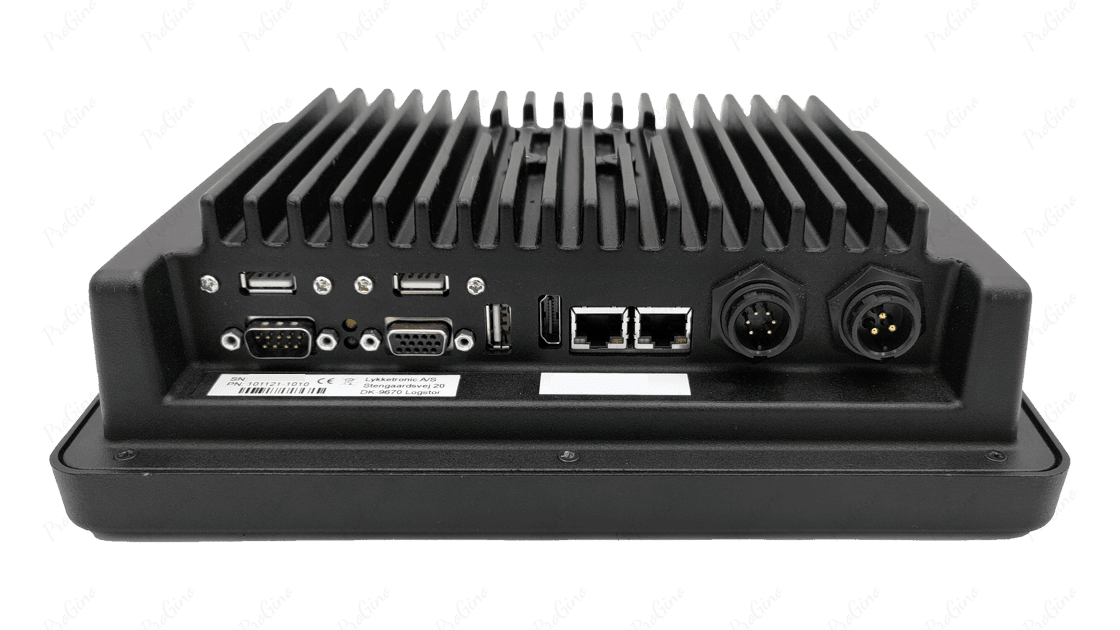